Неподалеку от Москвы, чуть в стороне от небольшого городка Лыткарино, над подмосковным лесом возвышается массивная 72-метровая башня, на стене которой изображен символ, очень напоминающий знаменитое «Всевидящее око». Но, конечно же, мистика к этому не имеет никакого отношения — это логотип Лыткаринского завода оптического стекла.
Хотя и «Всевидящее око» было бы здесь весьма уместно: ведь именно на ЛЗОС, входящем сейчас в состав холдинга «Швабе», изготавливают зеркала для самых больших телескопов мира, с помощью которых человечество заглядывает на миллиарды световых лет в глубины нашей Вселенной. Впрочем, на ЛЗОС делают не только зеркала и не только для телескопов: ассортимент оптических материалов, элементов и приборов насчитывает не одну сотню позиций.
На этом огромном станке сейчас установлено для реставрации шестиметровое первое главное зеркало (вверху) российского телескопа БТА (на самом телескопе используется второе главное зеркало). С его поверхности было удалено 8 мм стекла, в результате чего зеркало массой 42 т «похудело» на 500 кг. После переполировки зеркало будет возвращено в обсерваторию в Нижнем Архызе.
Все начинается с горшка
Путь любого оптического элемента начинается со стекловаренного сосуда (горшка). Это большой керамический тигель объемом 500 либо 700 л, который предварительно высушивают и обжигают в специальной печи («каленнице») при температуре около 1000 °C. После такого обжига сосуд переносят в газовую горшковую печь, разогревают до определенной температуры, а затем загружают стеклобой (остатки стекла того же сорта от предыдущих варок). Это стекло расплавляется и растекается по стенкам горшка, обеспечивая дополнительную защиту при варке.
Затем в стекловаренный сосуд загружают шихту — порошкообразную смесь оксида кремния (кварцевого песка), оксида свинца, борной кислоты, оксида (или гидроксида) алюминия и других ингредиентов (точная рецептура зависит от сорта стекла), после чего начинается процесс варки, продолжающийся обычно несколько суток.
Температура варки для различных сортов стекла различна: флинты (стекла с высоким показателем преломления, содержащие оксиды свинца) низкотемпературные, они варятся при 1400 °C, а кроны (натриево-силикатные стекла с низким показателем преломления) требуют более высоких температур, достигающих 1570 °C.
В процессе варки расплавленное стекло непрерывно перемешивают с помощью специальной керамической мешалки, чтобы стекло получилось гомогенным по химическому составу.
После обжига внутренние стенки горшка «обмазывают» стеклобоем – остатками от предыдущих варок того же сорта стекла. Это обеспечивает дополнительную защиту стенок горшка от агрессивной среды во время варки. Горшок обычно используется многократно – в нем можно варить стекло того же состава до 12 раз. А вот при варке высокотемпературных стекол горшка хватает всего на один раз.
Ничего лишнего
«Оптическое стекло должно содержать очень мало включений, буквально единицы на килограмм, — говорит начальник бюро стекловарения ЛЗОС Михаил Гулюкин. — Но при варке в стекломассе образуется множество пузырьков. Крупные пузыри всплывают, а вот мелкие нужно удалить. Для этого в конце варки на этапе так называемого осветления расплавленную стекломассу размешивают деревянной чуркой, вымоченной в воде, или, как делали это наши деды, сырой картофелиной.
Вода закипает, образуется много водяного пара и других газов, расплав бурлит, крупные пузыри поднимаются вверх, захватывая мелкие пузырьки и другие включения, — происходит, выражаясь техническим языком, процесс барботирования. Это бурление перемешивает расплав, помогая его гомогенизировать, то есть сделать однородным по составу и по температуре».
Когда процесс варки закончен, шаржирный кран вынимает горшок с расплавленным стеклом из печи и переносит его к месту литья в форму.
В процессе варки несколько раз берутся пробы стекломассы, которые контролируются на наличие включений. «Когда масса разогрета и светится, включения могут быть видны даже невооруженным глазом, — объясняет Михаил Гулюкин. — Но в любом случае после остывания образцы проверяют в лаборатории на специальном приборе — нефелометре, который измеряет рассеяние света на включениях в составе стекла». В процессе же самой варки в газовых горшковых печах автоматически контролируется более 20 параметров. Не менее строгий контроль и на других печах завода — с электрическим индукционным нагревом и небольших ванных.
Даже во время заполнения литейной формы важно не допускать неравномерного охлаждения различных областей, иначе в стекле появятся свили – оптические неоднородности, области с различными показателями преломления.
Медленно остыть
Когда варка заканчивается (на ЛЗОС говорят «закрывается»), к печи подъезжает шаржирный кран, предназначенный для загрузки и выгрузки горшков, и с помощью манипулятора вынимает горшок из печи. Горшок «отряхивают» от прилипшего к его дну песка (на подушке из которого он стоит в печи), а также удаляют «стяжку» — слегка остывшую верхнюю «корочку», в которой скапливается большинство включений, захваченных всплывающими пузырями. После этого расплавленное стекло выливают в форму.
Отжиг, то есть контролируемое охлаждение стеклянной отливки, – очень медленный процесс. Заготовки для крупных деталей, таких как зеркала из астроситалла диаметром 2–4 м, могут остывать в специальной печи по заданной программе на протяжении одного-двух лет.
«Включения не единственные дефекты оптического стекла, — говорит Михаил Гулюкин. — Если стекломассу плохо перемешать, то из-за неравномерности химического состава в стеклянной отливке образуются свили — области с другим показателем преломления. Оптические неоднородности в стекле могут возникнуть и по причине неравномерного охлаждения. Более того, при быстром охлаждении в стекле возникают значительные механические напряжения, которые могут просто разрушить стеклянную отливку».
Поэтому сразу после отлива форму с горячим полужидким стеклом помещают в специальную печь, где начинается грубый отжиг — так называется процесс очень медленного (буквально несколько градусов в сутки) контролируемого равномерного охлаждения отливки. Он занимает недели, порой месяцы, но затраты времени оправданны: при таком процессе внутренние напряжения минимизируются, так что по окончании отжига отливка остается целой (внутренние напряжения также влияют на оптическую однородность стекла).
Выборка с задней поверхности с помощью станка с ЧПУ, управляющего алмазной фрезой, позволяет облегчить деталь по сравнению со сплошной на 80%, превратив массив тяжелой стеклокерамики в ажурную, но жесткую конструкцию.
Тонкая наводка
После грубого отжига производится контроль отливки на специальном приборе — поляриметре, позволяющем визуализировать картину внутренних напряжений в поляризованном свете. Из отливки выбирают область с наименьшим количеством дефектов, вырезают ее и приступают к финальной стадии термообработки, тонкому отжигу.
Эта операция занимает около месяца, ее задача — придать заготовке равновесную структуру, чтобы температурные колебания как можно меньше влияли на оптические свойства. Для некоторых оптических материалов (в частности, стекол для светофильтров) во время тонкого отжига проводится операция «наводки» — специальная термообработка для создания упорядоченных структур, придающих стеклу нужные спектральные характеристики.
Рабочая поверхность зеркала после полировки контролируется с помощью интерферометра. На основе полученной интерферограммы создается программа управления для станка с ЧПУ. Точность обработки зеркал может составлять порядка десятков нанометров.
При охлаждении крупных (более 50 см) заготовок для деталей астрономических инструментов грубый и тонкий отжиг обычно совмещают. Для зеркал телескопов оптическая однородность материала отходит на второй план по сравнению с термомеханическими свойствами. Чтобы температура меньше влияла на форму зеркал, их изготавливают не из стекла, а из астроситалла, прочного стеклокерамического материала с почти нулевым коэффициентом температурного расширения.
Часть зеркал, установленных на стендах в цехе финишной обработки, предназначены не для телескопов – это вспомогательные зеркала систем оптического контроля изготавливаемой оптики.
Надежный тыл
Но пока что мы имели дело только с блоком из оптического стекла или стеклокерамики. Чтобы превратить его в деталь оптического инструмента, нужно придать его рабочей поверхности нужную форму (для телескопов обычно вогнутую сферическую или асферическую). «Обработку крупных зеркал начинают с задней поверхности, — рассказывает инженер-конструктор конструкторско-технологического бюро НПК-95 (научно-производственного комплекса) крупногабаритной оптики ЛЗОС Николай Добриков. — Задача — получить не просто зеркало, а максимально легкое и максимально жесткое зеркало, поэтому мы на станках с ЧПУ с помощью алмазных фрез выбираем лишний материал с тыльной поверхности, создавая вместо сплошного массива ажурную жесткую несущую структуру. Сейчас таким способом мы можем облегчить зеркало на 80% по сравнению со сплошным». Заднюю поверхность шлифуют или полируют — иногда на нее крепят дополнительные датчики или оптические элементы, необходимые для юстировки.
Башня, возвышающаяся над территорией завода на семьдесят с лишним метров, построена вовсе не для красоты. Внутри сооружения расположена вакуумная камера высотой 72 м для измерения различных характеристик крупных длиннофокусных зеркал. Испытания в вакууме позволяют нивелировать влияние потоков воздуха и пыли и тем самым значительно повысить точность измерений.
Свет мой, зеркальце
Обработка поверхности начинается с придания ей первоначальной формы — вогнутой сферической или асферической — в виде небольших ступенек на станках с ЧПУ. Затем ступеньки сошлифовываются, рабочую поверхность постепенно выравнивают, переходя на более мелкий абразив, и полируют. «Отклонение от заданной поверхности для зеркала телескопа должно быть порядка десятков нанометров, — говорит Николай Добриков. — Поэтому после каждого этапа полировки точность обработки контролируется интерферометром, а полученная интерферограмма расшифровывается в карту поверхности, на основании которой составляется программа обработки для станка с ЧПУ».
Полировать зеркала можно не только механически. В соседнем цехе расположена установка ионно-лучевой обработки, которая полирует поверхность пучком ионов аргона и ксенона. А рядом — камера напыления покрытий, где на уже готовую плоскость зеркала с помощью магнетронного распыления в скрещенных электрических и магнитных полях наносят многослойные (сотни слоев толщиной порядка 2 нм каждый) покрытия, которые и будут отражать свет далеких звезд.
Для просмотра ссылки необходимо нажать
Вход или Регистрация
Хотя и «Всевидящее око» было бы здесь весьма уместно: ведь именно на ЛЗОС, входящем сейчас в состав холдинга «Швабе», изготавливают зеркала для самых больших телескопов мира, с помощью которых человечество заглядывает на миллиарды световых лет в глубины нашей Вселенной. Впрочем, на ЛЗОС делают не только зеркала и не только для телескопов: ассортимент оптических материалов, элементов и приборов насчитывает не одну сотню позиций.
Для просмотра ссылки необходимо нажать
Вход или Регистрация
Для просмотра ссылки необходимо нажать
Вход или Регистрация
Для просмотра ссылки необходимо нажать
Вход или Регистрация
Для просмотра ссылки необходимо нажать
Вход или Регистрация
Для просмотра ссылки необходимо нажать
Вход или Регистрация
Для просмотра ссылки необходимо нажать
Вход или Регистрация
На этом огромном станке сейчас установлено для реставрации шестиметровое первое главное зеркало (вверху) российского телескопа БТА (на самом телескопе используется второе главное зеркало). С его поверхности было удалено 8 мм стекла, в результате чего зеркало массой 42 т «похудело» на 500 кг. После переполировки зеркало будет возвращено в обсерваторию в Нижнем Архызе.
Для просмотра ссылки необходимо нажать
Вход или Регистрация
Все начинается с горшка
Путь любого оптического элемента начинается со стекловаренного сосуда (горшка). Это большой керамический тигель объемом 500 либо 700 л, который предварительно высушивают и обжигают в специальной печи («каленнице») при температуре около 1000 °C. После такого обжига сосуд переносят в газовую горшковую печь, разогревают до определенной температуры, а затем загружают стеклобой (остатки стекла того же сорта от предыдущих варок). Это стекло расплавляется и растекается по стенкам горшка, обеспечивая дополнительную защиту при варке.
Затем в стекловаренный сосуд загружают шихту — порошкообразную смесь оксида кремния (кварцевого песка), оксида свинца, борной кислоты, оксида (или гидроксида) алюминия и других ингредиентов (точная рецептура зависит от сорта стекла), после чего начинается процесс варки, продолжающийся обычно несколько суток.
Температура варки для различных сортов стекла различна: флинты (стекла с высоким показателем преломления, содержащие оксиды свинца) низкотемпературные, они варятся при 1400 °C, а кроны (натриево-силикатные стекла с низким показателем преломления) требуют более высоких температур, достигающих 1570 °C.
В процессе варки расплавленное стекло непрерывно перемешивают с помощью специальной керамической мешалки, чтобы стекло получилось гомогенным по химическому составу.
После обжига внутренние стенки горшка «обмазывают» стеклобоем – остатками от предыдущих варок того же сорта стекла. Это обеспечивает дополнительную защиту стенок горшка от агрессивной среды во время варки. Горшок обычно используется многократно – в нем можно варить стекло того же состава до 12 раз. А вот при варке высокотемпературных стекол горшка хватает всего на один раз.
Для просмотра ссылки необходимо нажать
Вход или Регистрация
Ничего лишнего
«Оптическое стекло должно содержать очень мало включений, буквально единицы на килограмм, — говорит начальник бюро стекловарения ЛЗОС Михаил Гулюкин. — Но при варке в стекломассе образуется множество пузырьков. Крупные пузыри всплывают, а вот мелкие нужно удалить. Для этого в конце варки на этапе так называемого осветления расплавленную стекломассу размешивают деревянной чуркой, вымоченной в воде, или, как делали это наши деды, сырой картофелиной.
Вода закипает, образуется много водяного пара и других газов, расплав бурлит, крупные пузыри поднимаются вверх, захватывая мелкие пузырьки и другие включения, — происходит, выражаясь техническим языком, процесс барботирования. Это бурление перемешивает расплав, помогая его гомогенизировать, то есть сделать однородным по составу и по температуре».
Когда процесс варки закончен, шаржирный кран вынимает горшок с расплавленным стеклом из печи и переносит его к месту литья в форму.
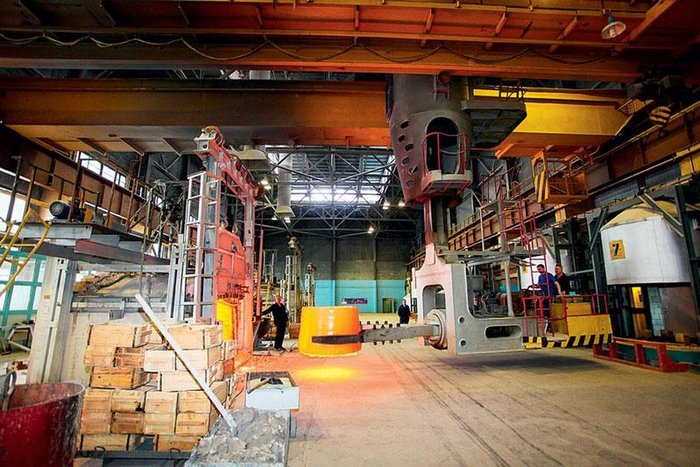
В процессе варки несколько раз берутся пробы стекломассы, которые контролируются на наличие включений. «Когда масса разогрета и светится, включения могут быть видны даже невооруженным глазом, — объясняет Михаил Гулюкин. — Но в любом случае после остывания образцы проверяют в лаборатории на специальном приборе — нефелометре, который измеряет рассеяние света на включениях в составе стекла». В процессе же самой варки в газовых горшковых печах автоматически контролируется более 20 параметров. Не менее строгий контроль и на других печах завода — с электрическим индукционным нагревом и небольших ванных.
Даже во время заполнения литейной формы важно не допускать неравномерного охлаждения различных областей, иначе в стекле появятся свили – оптические неоднородности, области с различными показателями преломления.
Для просмотра ссылки необходимо нажать
Вход или Регистрация
Медленно остыть
Когда варка заканчивается (на ЛЗОС говорят «закрывается»), к печи подъезжает шаржирный кран, предназначенный для загрузки и выгрузки горшков, и с помощью манипулятора вынимает горшок из печи. Горшок «отряхивают» от прилипшего к его дну песка (на подушке из которого он стоит в печи), а также удаляют «стяжку» — слегка остывшую верхнюю «корочку», в которой скапливается большинство включений, захваченных всплывающими пузырями. После этого расплавленное стекло выливают в форму.
Отжиг, то есть контролируемое охлаждение стеклянной отливки, – очень медленный процесс. Заготовки для крупных деталей, таких как зеркала из астроситалла диаметром 2–4 м, могут остывать в специальной печи по заданной программе на протяжении одного-двух лет.
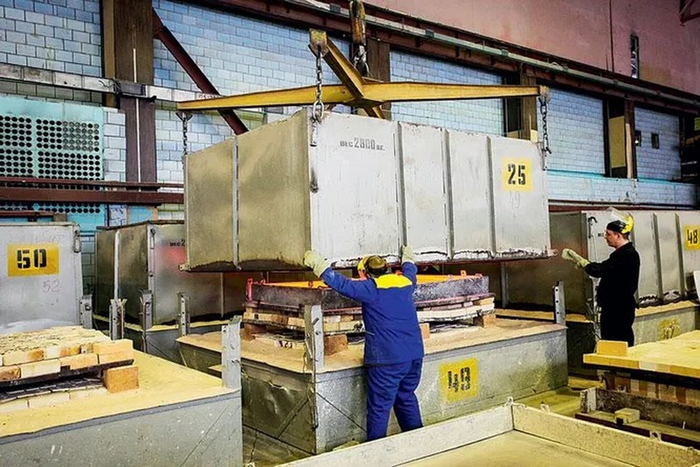
«Включения не единственные дефекты оптического стекла, — говорит Михаил Гулюкин. — Если стекломассу плохо перемешать, то из-за неравномерности химического состава в стеклянной отливке образуются свили — области с другим показателем преломления. Оптические неоднородности в стекле могут возникнуть и по причине неравномерного охлаждения. Более того, при быстром охлаждении в стекле возникают значительные механические напряжения, которые могут просто разрушить стеклянную отливку».
Поэтому сразу после отлива форму с горячим полужидким стеклом помещают в специальную печь, где начинается грубый отжиг — так называется процесс очень медленного (буквально несколько градусов в сутки) контролируемого равномерного охлаждения отливки. Он занимает недели, порой месяцы, но затраты времени оправданны: при таком процессе внутренние напряжения минимизируются, так что по окончании отжига отливка остается целой (внутренние напряжения также влияют на оптическую однородность стекла).
Выборка с задней поверхности с помощью станка с ЧПУ, управляющего алмазной фрезой, позволяет облегчить деталь по сравнению со сплошной на 80%, превратив массив тяжелой стеклокерамики в ажурную, но жесткую конструкцию.
Для просмотра ссылки необходимо нажать
Вход или Регистрация
Тонкая наводка
После грубого отжига производится контроль отливки на специальном приборе — поляриметре, позволяющем визуализировать картину внутренних напряжений в поляризованном свете. Из отливки выбирают область с наименьшим количеством дефектов, вырезают ее и приступают к финальной стадии термообработки, тонкому отжигу.
Эта операция занимает около месяца, ее задача — придать заготовке равновесную структуру, чтобы температурные колебания как можно меньше влияли на оптические свойства. Для некоторых оптических материалов (в частности, стекол для светофильтров) во время тонкого отжига проводится операция «наводки» — специальная термообработка для создания упорядоченных структур, придающих стеклу нужные спектральные характеристики.
Рабочая поверхность зеркала после полировки контролируется с помощью интерферометра. На основе полученной интерферограммы создается программа управления для станка с ЧПУ. Точность обработки зеркал может составлять порядка десятков нанометров.
Для просмотра ссылки необходимо нажать
Вход или Регистрация
При охлаждении крупных (более 50 см) заготовок для деталей астрономических инструментов грубый и тонкий отжиг обычно совмещают. Для зеркал телескопов оптическая однородность материала отходит на второй план по сравнению с термомеханическими свойствами. Чтобы температура меньше влияла на форму зеркал, их изготавливают не из стекла, а из астроситалла, прочного стеклокерамического материала с почти нулевым коэффициентом температурного расширения.
Часть зеркал, установленных на стендах в цехе финишной обработки, предназначены не для телескопов – это вспомогательные зеркала систем оптического контроля изготавливаемой оптики.
Для просмотра ссылки необходимо нажать
Вход или Регистрация
Надежный тыл
Но пока что мы имели дело только с блоком из оптического стекла или стеклокерамики. Чтобы превратить его в деталь оптического инструмента, нужно придать его рабочей поверхности нужную форму (для телескопов обычно вогнутую сферическую или асферическую). «Обработку крупных зеркал начинают с задней поверхности, — рассказывает инженер-конструктор конструкторско-технологического бюро НПК-95 (научно-производственного комплекса) крупногабаритной оптики ЛЗОС Николай Добриков. — Задача — получить не просто зеркало, а максимально легкое и максимально жесткое зеркало, поэтому мы на станках с ЧПУ с помощью алмазных фрез выбираем лишний материал с тыльной поверхности, создавая вместо сплошного массива ажурную жесткую несущую структуру. Сейчас таким способом мы можем облегчить зеркало на 80% по сравнению со сплошным». Заднюю поверхность шлифуют или полируют — иногда на нее крепят дополнительные датчики или оптические элементы, необходимые для юстировки.
Башня, возвышающаяся над территорией завода на семьдесят с лишним метров, построена вовсе не для красоты. Внутри сооружения расположена вакуумная камера высотой 72 м для измерения различных характеристик крупных длиннофокусных зеркал. Испытания в вакууме позволяют нивелировать влияние потоков воздуха и пыли и тем самым значительно повысить точность измерений.
Для просмотра ссылки необходимо нажать
Вход или Регистрация
Свет мой, зеркальце
Обработка поверхности начинается с придания ей первоначальной формы — вогнутой сферической или асферической — в виде небольших ступенек на станках с ЧПУ. Затем ступеньки сошлифовываются, рабочую поверхность постепенно выравнивают, переходя на более мелкий абразив, и полируют. «Отклонение от заданной поверхности для зеркала телескопа должно быть порядка десятков нанометров, — говорит Николай Добриков. — Поэтому после каждого этапа полировки точность обработки контролируется интерферометром, а полученная интерферограмма расшифровывается в карту поверхности, на основании которой составляется программа обработки для станка с ЧПУ».
Для просмотра ссылки необходимо нажать
Вход или Регистрация
Полировать зеркала можно не только механически. В соседнем цехе расположена установка ионно-лучевой обработки, которая полирует поверхность пучком ионов аргона и ксенона. А рядом — камера напыления покрытий, где на уже готовую плоскость зеркала с помощью магнетронного распыления в скрещенных электрических и магнитных полях наносят многослойные (сотни слоев толщиной порядка 2 нм каждый) покрытия, которые и будут отражать свет далеких звезд.
Для просмотра ссылки необходимо нажать
Вход или Регистрация